Technologia i historia grupy Gealan
Grupa GEALAN
Ekstruzja czy też ekstrudowanie oznacza ciągły proces wytłaczania pasm z plastycznych tworzyw lub ich produktów wstępnych (np. granulatu). Twarda z początku masa ekstrudowana, dzięki ogrzewaniu, zagęszczaniu i ścinaniu zamienia się w jednolite topliwo, to znaczy masa ekstrudowana poddawana jest uplastycznieniu.
Aby można było rozpocząć proces ekstruzji, samochody ciężarowe muszą dostarczyć niezbędne surowce. Po przejściu kontroli towarów wchodzących różne komponenty (PVC, kreda i dwutlenek tytanu) wzbogaca się w mieszalni o pewne dodatki zgodnie ze specjalną recepturą GEALAN. W ramach dwóch oddzielnie sterowanych linii mieszania odbywa się automatyczne ważenie surowców, dodawanie wewnętrznego materiału obiegowego, oraz transportowanie, dozowanie, mieszanie, suszenie i schładzanie materiału. Gotowy, wymieszany materiał transportowany jest do silosu dziennego i jest już przygotowany do właściwego procesu ekstruzji.
Pierwszy ekstrudowany profil okienny opuścił zakład GEALAN w 1968 roku. Od tamtej pory trwa ciągły rozwój i udoskonalanie procesu ekstruzji, czego dowodzą m.in. koekstrudowane profile okienne.
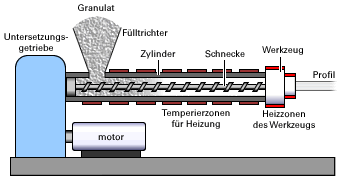
Aparatura do ekstruzji ? oprócz samego ekstrudera i narzędzia ? obejmuje urządzenia linii ekstruzyjnej, gdzie dokonuje się kalibracja ekstrudatu, schładzanie, odciąganie, cięcie na długość i odkładanie. Wszystkie urządzenia linii ekstruzyjnej muszą być technicznie dostosowane do danej zdolności przepustowej ekstrudera. Tak na przykład gorący i niestabilny profil ? po wyjściu z narzędzia ? musi zostać schłodzony w procesie kalibracji i tam też uzyskuje ostateczny kształt. W strefie kalibracji wytwarzana jest próżnia, co powoduje dociśnięcie powierzchni zewnętrznych profilu do ścianek strefy kalibracji. Po przejściu wypełnionej wodą łaźni schładzającej i mechanizmu odciągającego, po wewnętrznej i zewnętrznej stronie profilu nakładana jest folia ochronna, zanim zostanie on pocięty na sześciometrowe kawałki w urządzeniu tnącym. Potem urządzenie sortujące automatycznie pakuje profile do kontenera. Po zapakowaniu kontenera profile albo składuje się w centrum logistyki, albo wysyła natychmiast samochodem ciężarowym do klienta.
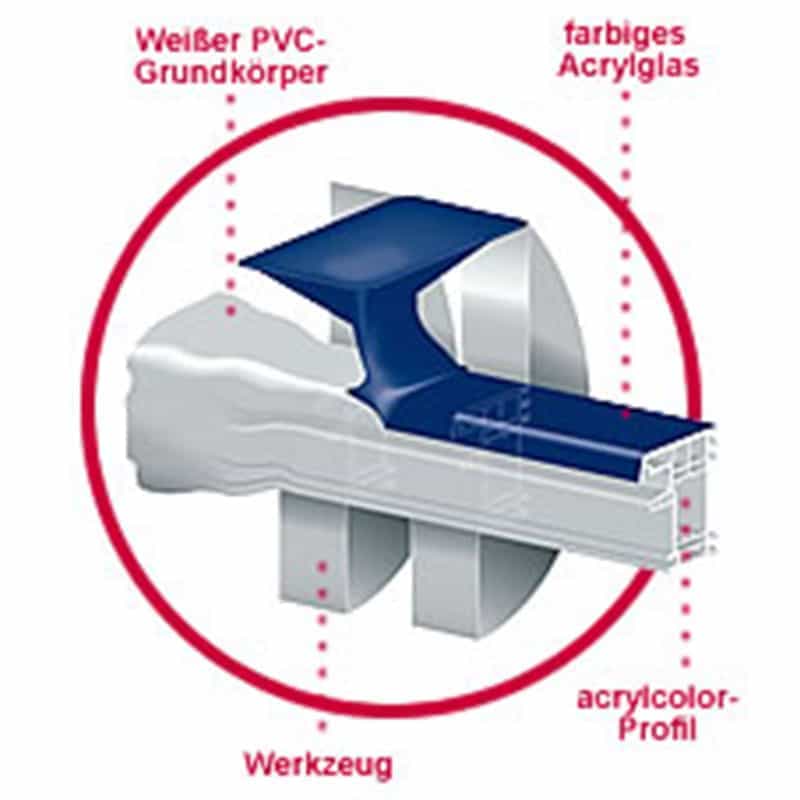
W przypadku koekstruzji rdzeń profilu, w tym stanie obróbki składający się z białego płynnego topliwa PVC, łączony jest nierozerwalnie z barwnym płynnym topliwem akrylowym. Proces ten odbywa się w narzędziu koesktruzji, do którego, oprócz głównego ekstrudera, podłączony jest drugi ekstruder, doprowadzający do narzędzia topliwo akrylowe. Barwne topliwo akrylowe jest dokładnie nanoszone na tę powierzchnię profilu, która potem w gotowym oknie wystawiona będzie na działania czynników atmosferycznych, czyli słońca, światła, deszczu i śniegu. Profil acrylcolor opuszczający dyszę koekstrudera jest już dwukolorowy. Dzięki kombinacji różnych tworzyw (PVC i akryl) uzyskuje się produkt, w którym wymagane cechy użytkowe prezentują wyższą jakość. Proces koekstruzji zapewnia niezrównaną trwałość kolorów. Przy sukcesywnej wymianie jednostek okiennych w jednej i tej samej bryle budynku różnice wizualne, nawet po wielu latach, pozostają niemal niedostrzegalne.
Koekstruzję stosuje się w firmie GEALAN od 1980 roku. Potwierdzeniem niezaprzeczalnych osiągnięć na tym polu są znaki jakości RAL dla profili acrylcolor oraz znak jakości Południowo-Niemieckiego Centrum Tworzyw Sztucznych.
Kluczowe technologie – STV? ? suche szklenie statyczne.
STV? ? suche szklenie statyczne to innowacyjna technologia klejenia szyb wykorzystywana w procesie produkcji okien. Tajemnica STV? kryje się w specjalnie opracowanej taśmie, która w procesie ekstruzji trwale przymocowywana jest do przylgi skrzydła. Producent okien otrzymuje jeden produkt ? skrzydło z taśmą STV?. Obróbka profili z taśmą STV? przebiega w tradycyjny sposób i niepotrzebne są żadne inwestycje w dodatkowe maszyny. Przycinanie, zgrzewanie, zaczyszczanie oraz szklenie wymaga tylko drobnych zmian w ustawieniach parametrów maszyn do produkcji okien.
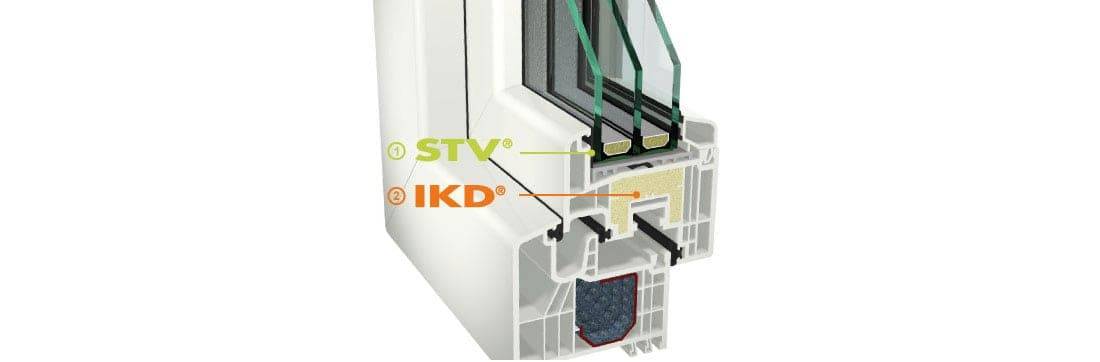
Większe okna, lepszy współczynnik Uf , większe bezpieczeństwo!
Jednoczesne zastosowanie STV? oraz wzmocnienia stalowego w skrzydle umożliwia budowę okien o naprawdę dużych rozmiarach, które jeszcze niedawno wydawały się niemożliwe i poprawia właściwości użytkowe okien. Ponadto w kontekście STV? przy użyciu wzmocnień izolowanych termicznie mogą być budowane wyjątkowo ciepłe i stabilne okna o normalnych rozmiarach. STV może być również stosowane w oknach giętych poprawiając tym samych ich stabilność.
Stosowanie STV? przy jednoczesnym zrezygnowaniu ze wzmocnienia stalowego w skrzydle istotnie wpływa na współczynnik Uf. Zważywszy na to, że normalnej wielkości okna można budować bez stali w skrzydle prowadzi to do obniżenia współczynnika Uf średnio o 0,2 W/(m??K) dla danej kombinacji profili.
Ponadto duża powierzchnia klejenia szyby do przylgi skrzydła polepsza ochronę przed włamywaczami. Wywarzenie szyby jest dodatkowo utrudnione.
Stosowanie STV? przy jednoczesnym zrezygnowaniu ze wzmocnienia stalowego w skrzydle istotnie wpływa na współczynnik Uf. Zważywszy na to, że normalnej wielkości okna można budować bez stali w skrzydle prowadzi to do obniżenia współczynnika Uf średnio o 0,2 W/(m??K) dla danej kombinacji profili.
Ponadto duża powierzchnia klejenia szyby do przylgi skrzydła polepsza ochronę przed włamywaczami. Wywarzenie szyby jest dodatkowo utrudnione.
Kluczowe technologie – IKD? ? podwyższona izolacja rdzenia.
Interesującym sposobem na obniżenie współczynnika Uf jest wypełnienie piankowe profili. Nowa technologia klejenia szyb na sucho ? STV? stwarza w tej dziedzinie nowe perspektywy. Duża powierzchnia klejenia szyby i przylgi skrzydła specjalną taśmą STV? sprawia, że wzmocnienie stalowe w skrzydle nie jest już konieczne. Powstała w ten sposób pusta komora główna w skrzydle może być wykorzystana w celu podniesienia izolacji cieplnej. Głównym założeniem połączenia technologii STV i IKD? było osiągnięcie współczynnika Uw na poziomie poniżej 0,80 W/(m??K) ? a więc standardu wymaganego dla domów pasywnych.
Profile z IKD? bezpośrednio od GEALAN
Aby osiągnąć założone cele konieczne było stworzenie takiego wypełnienia, które będzie się zgrzewać. Ponadto konstruktorzy GEALAN opracowali metodę produkcji, która już na etapie ekstruzji profilu pozwala wypełniać profile pianą. Oznacza to, że producent okien nie musi ponosić żadnych kosztów związanych z inwestycją w dodatkowe maszyny, ponieważ otrzymuje on sztangi profili fabrycznie wypełnione pianką. Kolejne etapy produkcji okien takie jak przycinanie, czy zgrzewanie przebiegają zupełnie normalnie.