History and technology of Gealan
Group GEALAN
To begin the process of extrusion, trucks must provide the necessary raw materials. After passing inspection of goods entering various components (PVC, chalk and titanium dioxide) is enriched in the mixing of certain additives according to a special recipe GEALAN. In two separately controlled mixing line performs an automatic weighing of raw materials, adding an internal recycle material, and transporting, dispensing, mixing, drying and cooling of the material. Ready mixed material is transported to the silo daily and is already prepared for the proper extrusion process.
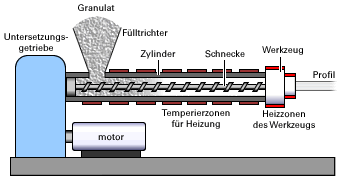
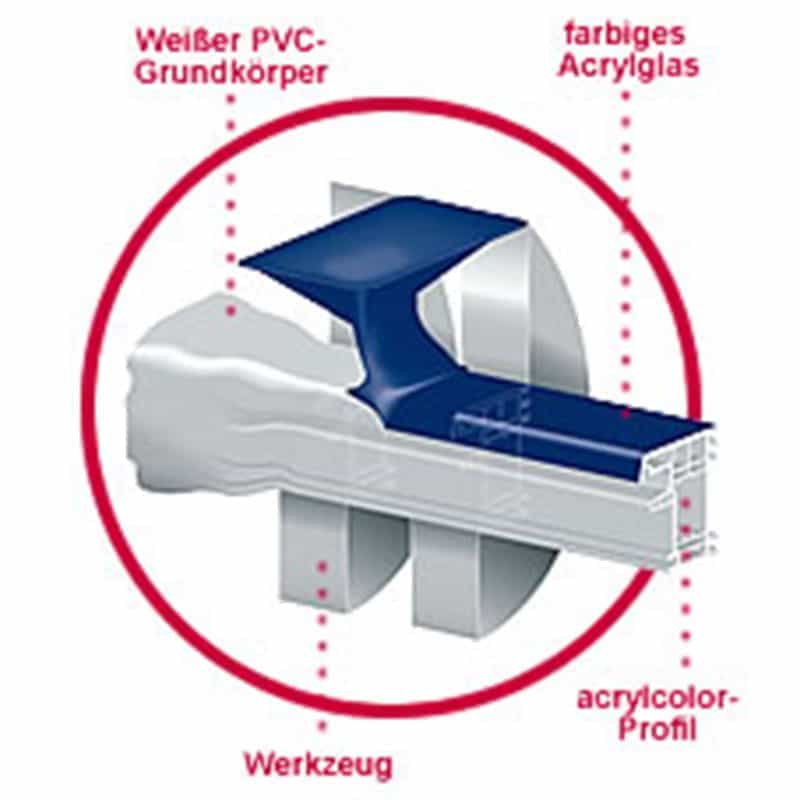
Key technologies – STV? – static dry glazing.
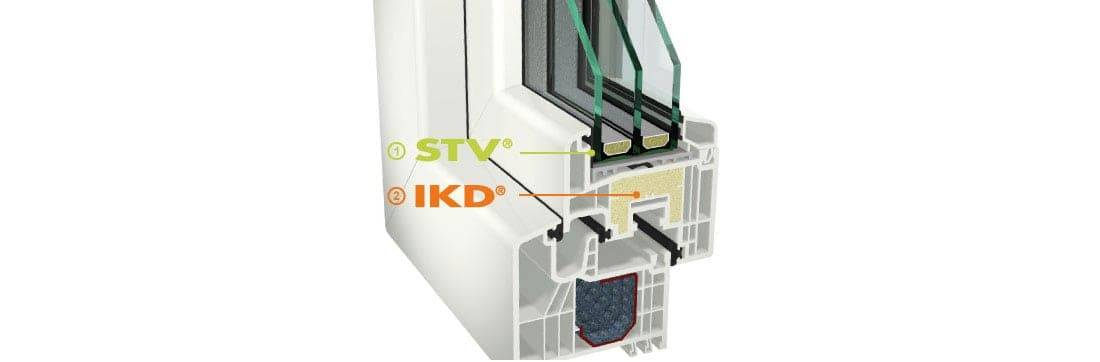
Larger windows, better Uf factor, more safety!
Simultaneous use of STV? and steel reinforcements in the door leaf allows the construction of windows in the really big sizes, which seemed impossible recently. It also improves the performance of windows. Furthermore, in the context of STV? using thermally insulated reinforcements it is possible be built exceptionally warm and stable windows of stabdard sizes. STV may also be used in the curved windows with improved stability.
The use of STV? while resigning from the steel reinforcement in the leaf significantly affect the Uf factor. Given that the normal window size can be built without steel in the windows leaf leads to a reduction of Uf in 0.2 W / (m? ? K) (in average ) for a given combination of profiles.
In addition, a large area of bonding the glass to the sash improves protection against burglars. Forcing the glass is much more difficult.